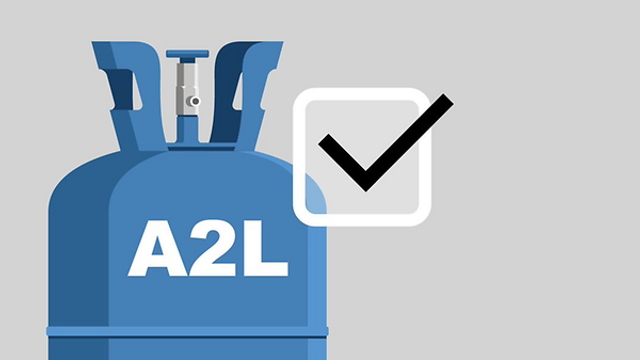
The transition to A2L refrigerants marks a significant shift in the HVAC and refrigeration industries, driven by the need for more environmentally friendly alternatives. A2L refrigerants, known for their lower global warming potential (GWP), are being adopted to replace older, more harmful refrigerants. As this transition unfolds, the role of plastic injection molding becomes increasingly important in producing components that can withstand the unique challenges posed by these new refrigerants. For those navigating the A2L refrigerant transition, https://www.galarson.com/ provides essential guidance and support to ensure a smooth and successful adaptation to these new standards.
Understanding A2L Refrigerants
A2L refrigerants are classified as mildly flammable with a low GWP, making them an attractive option for reducing the environmental impact of HVAC and refrigeration systems. However, their flammability and chemical properties require specific considerations when designing and manufacturing components. This is where plastic injection molding plays a crucial role.
Why Plastic Injection Molding is Essential for A2L Refrigerants
Plastic injection molding is vital in producing the high-performance components needed to handle A2L refrigerants. These components must meet stringent requirements for safety, durability, and chemical resistance. The ability of injection molding to produce complex, high-precision parts makes it the ideal manufacturing process for these applications.
1. Material Selection for A2L-Compatible Components
Selecting the right materials is critical when molding and assembling plastic components for use with A2L refrigerants. These materials must resist the refrigerants’ chemical properties and withstand the operating temperatures and pressures typical of HVAC systems. Advanced plastics such as polyamides (nylons), polyoxymethylene (POM), and thermoplastic elastomers (TPE) are often used in these applications due to their strength, durability, and resistance to chemicals.
2. Ensuring Component Integrity
The integrity of molded components is paramount when dealing with A2L refrigerants. Any flaws or weaknesses could lead to leaks or failures, posing safety risks. Plastic injection molding offers the precision and control needed to produce defect-free parts that meet strict safety and performance standards. This precision is achieved through meticulous mold design, process control, and material selection, ensuring that each component can reliably withstand the demands of its application.
The Future of Plastic Injection Molding in the A2L Transition
As the industry continues to move toward A2L refrigerants, the demand for high-quality molded components will only grow. Innovations in plastic injection molding, including advancements in materials and processing technologies, will play a key role in meeting this demand. Manufacturers will need to stay ahead of the curve by investing in the latest equipment and techniques to produce parts that meet the evolving needs of the HVAC and refrigeration industries.
The Rise of A2L Refrigerants
Did you know that the push for A2L refrigerants is part of a global effort to phase out high-GWP refrigerants under international agreements like the Kigali Amendment? This transition is not only about meeting regulatory requirements but also about making a positive impact on the environment by reducing greenhouse gas emissions.
The transition to A2L refrigerants presents both challenges and opportunities for the HVAC and refrigeration industries. Plastic injection molding stands out as a crucial process in this transition, enabling the production of components that meet the stringent requirements of A2L refrigerants. By selecting the right materials, ensuring component integrity, and embracing innovative molding techniques, manufacturers can play a key role in advancing this important environmental initiative. As we move forward, the collaboration between material scientists, engineers, and molders will be essential in shaping a more sustainable future for refrigeration and beyond.